The concept of ‘digital twins’ is perceived as a revolutionary trend, expected to be increasing its role in the development of our civilisation in the near future. Sounds great, but what does airborne laser scanning technology have to do with it?
LiDAR technology (Light Detection and Ranging) fits well the global and rapidly developing idea of digital twins. In this respect, everything that surrounds us has its reflection in a point cloud – something MGGP Aero have been dealing with for 10 years, constantly expanding their experience and competence. Being part of the market, we realise how essential and valuable this type of data is. Also, a good opportunity to broaden and exchange one’s experience are meetings with the direct recipients of digital information, such as the recent 1st National LiDAR Users Forum– POLSCAN, gathering nearly 250 laser scanning specialists and enthusiasts.

The beginning
Our adventure with laser scanners began in 2009, when we mounted our first Riegl LMS Q680 on the airplane. We took to our new LiDAR passenger immediately. It impressed us with its efficiency and ability to penetrate vegetation layers and measure points with unprecedented density, even in hard-to-reach areas. We started developing numerous ideas of how we were going to use such promising data. Some of us concluded that point cloud emerged as an intriguing rival to aerial imagery, whereas others considered both technologies complementary.
With our first scanner purchase, we had already decided to set long-term relations with a reliable Austrian device supplier – Riegl who has released many interesting models over the last 10 years, achieving huge global success. Overall, we have used 6 various types of Riegl scanners, from the simplest light VUX to the latest bathymetric VQ-880. All our devices are equipped with INS/GPS system, integrated with various sensors to work on different kinds of aircraft. From the very start Riegl scanners have been an essential element of our multisensor photogrammetric platforms, used in most advanced projects involving simultaneous collection of a point cloud, aerial and oblique imagery or hyperspectral data.

Applications
Riegl scanners are well suited not only to projects focused on large areas. Our order book has been recording an increasing interest in low-altitude corridor mapping for narrow linear objects. These orders usually revolve around power, road or gas infrastructure management – so far we have completed projects with the overall length of more than 200,000 kilometres (as much as 5 lengths of the equator). We can also see LiDAR technologies being applied in archaeology, environmental protection, projects for local governments or nation-wide projects concerning creation of elevation databases in Europe (e.g., Polish ISOK/CAPAP).
The projects we have participated in covered the areas of several dozen up to several dozen thousand square kilometres, and the total area we have scanned so far has already exceeded 300,000 square kilometres (almost the area of Poland). We have also been active on foreign markets, among others, in Romania, Bulgaria, North Macedonia, Germany, Sweden, Norway, Finland, Estonia, Latvia and Lithuania.
Development
In the field of laser scanning, the rule of adapting the technology to the client’s demands (the market), proved to be right. These days modern laser scanners, aircraft or even specialist photogrammetric helicopters alone are not a guarantee of success. Since projects have become more complex and unique in recent years, they require flexibility in terms of modification and adjustment of hardware platforms. It is beyond doubt that producers are able to offer a lot of various sensors, with wide spectrum of possible modifications, to meet the client’s needs, however, it is not what innovation is about nowadays.
The clue is not to possess a modern laser scanner but to know how to use it effectively in practice. As an example we can use the integration of two extremely efficient sensors, which was a large-format photogrammetric camera and a laser scanner, mounted on a specially adapted aircraft. What we did was the world’s first ever recorded case of applying such a configuration during one flight. Thanks to it we obtained large-format imagery with 3cm GSD and laser scanning with a density of 12p/m2. But most importantly, this undertaking was not a part of any test or research but actual realisation of several projects at the same time, which consequently provided our clients with a unique dataset.

Revolution?
Only one conclusion can be drawn after the 1st National LiDAR Users Forum – POLSCAN, namely: there is no revolution. Nothing has changed significantly in that matter for years. The measurement parameters of laser scanners have only been refined. There are, however, some attempts to implement hybrid solutions, e.g. by combining different spectrum ranges (532nm, 1044nm, 1550nm). In recent years, the suppliers have, indeed, successfully improved the performance of their devices (e.g., Riegl VQ-1560 II has been equipped with two highly efficient scanners VQ-780 II). A laser operating at the frequency of 4 MHz performs measurements at a speed of up to 2,66 mill. p/s. I am sure some of you remember Riegl VQ-780, released between 2016 and 2017 – not so long ago its producers launched a new device that is four times more efficient!

Such a dynamic situation on the market does not allow the equipment to amortize because companies are constantly urged to keep abreast with the times by investing their money in newer ‘toys’. The use of new scanners translates into faster acquisition of data that can be performed from higher altitudes or with enhanced cruise speed, or even by increasing the point cloud density.
But faster does not always mean better…
Footprint and its size
This brings us to the problem of laser footprint. The pulse of a laser scanner is emitted towards the Earth’s surface with the speed of light. It reflects from the surface and, being recorded, travels back to the device. During its journey, the beam disperses, which means that the measurement does not concern one spot but a certain area whose shape can be compared more or less to an ellipse. The point cloud that we analyse later is nothing else but a representation of the centres of those ellipses.
So, what does the footprint size depend on? Does it affect the measurement results? It surely does, given the fact that the detailed national technical guidelines more and more frequently limit its size. This issue is widely discussed in European projects as well. The main factors influencing the footprint size are: flight altitude, scanning angle or divergence angle dependent on spectral bands (e.g. IR or green) and wavelength. The footprint shape itself results from the scanning angle, slope and elements of land cover. Its size and shape play a crucial role when it comes to precise measurements in horizontal and vertical dimension. It is due to the manner in which the location of the measured point within the footprint is read. To put it simply, its location is attributed to the centre of the footprint. If a small object is detected on the border of the footprint, its location is determined with error. Therefore the bigger footprint, the bigger potential error while determining the XYZ coordinates of an object. Such an effect might be marginal when the footprint is located in a completely flat area.

In the case of linear objects, it has been noted that bigger footprint (low power) causes objects or their details to be poorly detected. It must be pointed out that increasing of the power of laser beam is strictly limited by safety requirements.

For sure, the size of a footprint – by weakening the effectiveness of classification and detection algorithms – is important when data is applied for: biomass determination, vegetation analyses, micro-relief mapping, precise determination of overhead power lines route, roof pitch or ground surface.
In Europe, in turn, this issue was brought up some time ago, leading to clarification of many limitations relating to LiDAR projects. Larger footprint has a negative effect on the qualitative features of a point cloud. If we want to obtain measurements with better quality, we cannot just focus on increasing the point cloud density. What is more, it may turn out that costs of storage and work with a super dense point cloud are greater than the potential profit.
Closer to the ground
The future of this technology is predictable only to a certain extent. Soon, we should expect a tendency for increasing the density of airborne laser scanning, but within reason. What seems obvious is the fact that ALS will never be able to replace images, and that use and classification of a very dense point cloud will continue to pose a challenge for many years to come. Machine learning, as well as automation of data processing and analysing are going to be a serious support in that field.
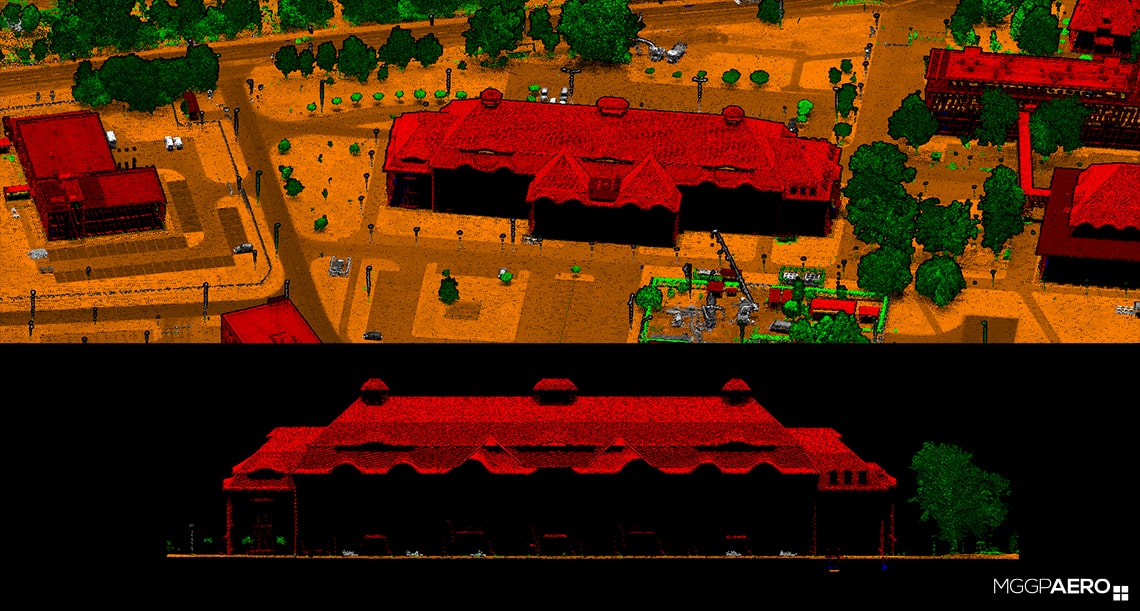
It can also be noticed that, apart from UAVs, using single scanners is not a common practice. Being relatively light, they are mounted in increasing numbers even on light aircraft. That is why many scanner producers have extended their offer to multi-sensor solutions, allowing collection of hybrid data.
The scanning performance of such devices is being continuously enhanced, but are we able to fly at even higher altitudes? Will the contractor, due to the size of the footprint, not make us fly closer to the ground? This is already happening with many European projects. Airborne laser scanning develops quickly in terms of efficiency, but in terms of new methods of application, it is not as dynamic. Today, it is hard to predict anything, only time will tell what the future holds.
Read on Linkedin